What are the advantages of cobots?
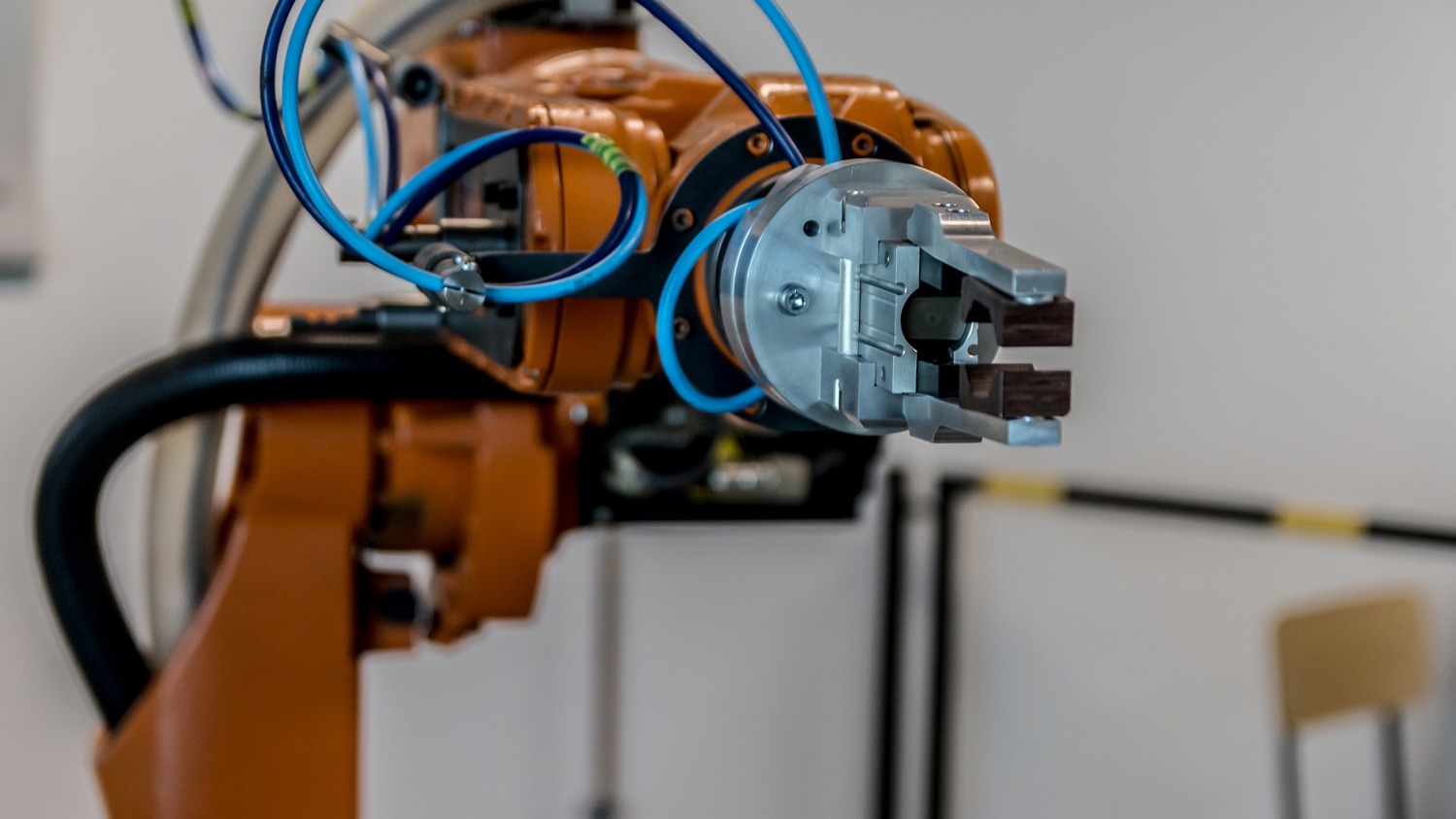
Afraid of robots? Meet the cobots!
Six questions to Dr. Matthias Hoffmann and Dr. Oliver Mueller from BEST, the Advice Centre for socially acceptable Technology-Designing in Saarbrücken, Germany
BEST is a partner in the Interreg North-West Europe COTEMACO (Increased NWE COmpetitiveness Through Efficient MAn & Machine COllaboration) project.
MH: Some tasks are better executed by robots, while others are better performed by a human being, for instance anything that requires flexibility, multidirectional work. Cobots match what human beings do best and what robots do best. This is why they are called cobots rather than robots. The work is also done faster with cobots. In shop floors for instance, technical mistakes linked to repetitive, precise, mechanical tasks are minimised which contributes to an increased production effectiveness. However, cobots bear both threats and opportunities. First there is a need to ensure the safety of employees by making sure they wouldn’t be physically hurt by the machine, nor alienated while working with them. Robot and human beings should not be competing with one another. Synergies, in the welding process for instance, are also developed so that the worker is more than just a supplier for the machine.
Is there a risk for workers to be entirely replaced by machines?
MH: The risk for workers to be replaced by machines has always been there. There were talks about factories without any humans 20 years ago. Our objective is to mitigate risks. While there is no way to change the course of technological development, it is possible to design processes which are beneficial to workers.
Tell us more about the COTEMACO project.
OM: In a few years, we’ve moved from tasks performed separately by robots and workers, to man-machine collaboration, with tasks being executed at the same time. Partners in the project are designing the terms of this collaboration, which is a new, specific working situation. Through COTEMACO, SMEs in the food manufacturing/processing and automotive sectors are provided with help to develop a man-machine collaboration tailored to their specific needs.
What are the benefits of having a variety of partners within the COTEMACO project?
OM: The eight different partners in the project bring complementary expertise: while some develop the technology, others help companies find the right business partners. At BEST, we provide advice to employee representatives. We train other partners and transfer our knowledge in the field of business counsel onto them. The successful implementation of a technology is also about having the concerned workers on board from the beginning to ensure a sustainable approach. Technologies can be well developed but if employees have not familiarised with them, they can be reluctant to working with them. ZeMA, the German Centre for Mechatronics and Automation Technology, asked us to join the project to develop strategies to get the workers involved, taking their views and experience into consideration. With four regions across North-West Europe involved (BE, UK, NL, DE), the project is reaching out to more companies than if it was a national initiative.
What challenges does COTEMACO face?
MH: The project needs to broaden the outreach of its voucher scheme to attract even more SMEs in its workshops. The technologies developed in the fields of Collaborative Robotics or Shop Floor Digitalisation will also have to be affordable otherwise companies won’t be able to sustain their costs.
What is the expected impact of the COTEMACO project?
OM: The SMEs enrolled in our support programme will start the use cases in our field labs and will be provided with guidelines to help them regarding the aspects to look at when developing a technology, what the risks and benefits are in order to evaluate if the technology matches with acceptable working conditions. By the end of the project in 2021, the participating SMEs will be able to increase their competitiveness through more efficient production. Changes in the labour market will occur as new jobs will replace low-skilled, repetitive tasks now performed by cobots. Workers whose tasks will have been taken over by the technology will therefore have new duties. The project should ideally result in the creation of additional jobs.